
IoTシステムの導入で不良率を軽減
発想力でDX化を実現
株式会社富士製作所 代表取締役社長 望月新史
東京都江戸川区小松川。小さな町工場の多いこの街で、長年、射出成型※1を専門とするプラスチック製品の加工・製造を行っているのが株式会社富士製作所だ。1953年の創業以来、地域に密着した下町の工場として、日本のものづくりに貢献している。富士製作所では、IoTネットワークシステムを導入して業務の効率化を実現。時間や人のムダを減らし、従業員の働き方まで改善させている。こうした多様な効果はどのようにして生み出されたのだろうか。望月新史社長に話を聞いた。
※1 加熱したプラスチックを金型に流し込むことで形作る成形法
-
株式会社富士製作所
代表取締役社長 望月 新史 -
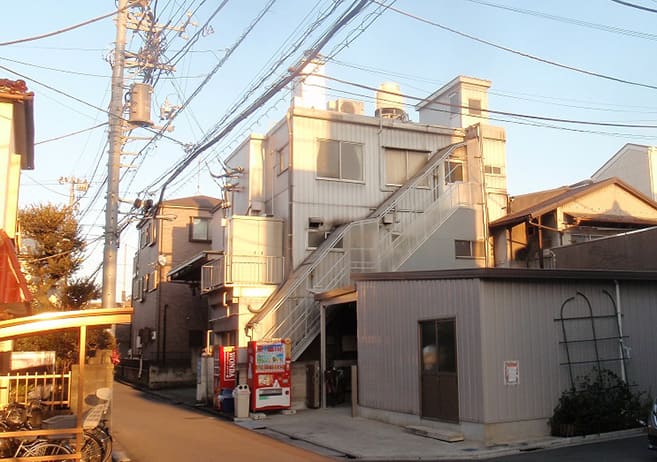
業種別DXのポイント
- 成型機とパソコンを繋ぎ、過去の生産経緯をデータとして蓄積
- 工程管理システムにより、バックオフィス業務をデジタル化
- 機械を自動化し、業務の効率化と働きやすい環境づくりを両立
若手が多い社風がDXを後押し
望月氏がDXに取り組むようになったのは、ご尊父である先代社長から会社を引き継いだ2015年頃のこと。それ以前から大型の成型機を導入していたものの作業効率が悪く、製品不良などのトラブルも少なくなかった。また、過去の作業実績をデータとして蓄積することができなかったので、不具合などが発生した際の原因解明が曖昧になってしまっていた。望月氏には、こうした業務を効率化して時間や人員のムダもなくしたいという想いがあった。
「その3年前の2012年頃から機械の自動化は少しずつ始めていて、徐々に独学で知識を深め、最新の成型機も導入しながら、絶対にこの会社を変えて行くんだと思っていました。2016年ごろから、私を含めて若い従業員が多くなり、ITやパソコンといったものに抵抗感がなかったのもDXを進める後押しになりました。業務もスムーズに引き継げたので、まずはできることからやってみようと」。
機械とパソコンを繋ぎ、生産経緯をデータとして蓄積
そこで新たに導入したのが、IoTネットワークによる成型機の統合管理システムだ。成型機をパソコンと繋ぐことで、過去の生産経緯がデータとして蓄積されていくので、新しい製品を作り始める場合でも短時間でセッティングが可能になる。樹脂を成型するためには、温度や圧力などの数値を製品ごとに機械に入力する必要があるのだが、蓄積されたデータを簡単に呼び出すことができるため、すぐに適切な数値で稼働できる。現在10台のうち8台がネットワークで繋がっており、仕事の効率を格段に向上させている。
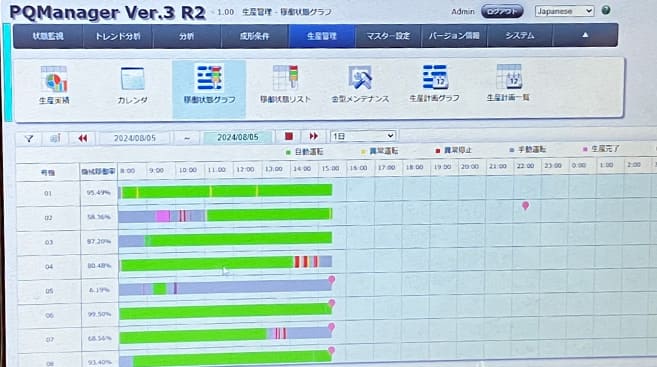
また、機械を自動化したことでムダな工程がなくなった。そのひとつが、樹脂をカットする工程だ。0.1ミリ刻みという高精度の仕上がりが自動で実現できるため、従業員を配置する必要がなくなった。その時間を活用して製品の袋詰めや台紙の貼り付け等を行う「後工程」まで請け負えるようになり、結果的に会社の売上も上がった。
「不良品が出てしまった場合でも、この日のこの工程のこの数値が乱れたから不良になった、という原因が明確に特定できるので取引先にも説明がしやすくなりました。裏付けとなるデータが提示できるので説得力があります。お客様の品質に求めるレベルが年々高くなっていることもありますが、原因解明を正確にやっておかないと私たちも納得できませんから。おかげでトラブルの数はほとんどなくなりました」。
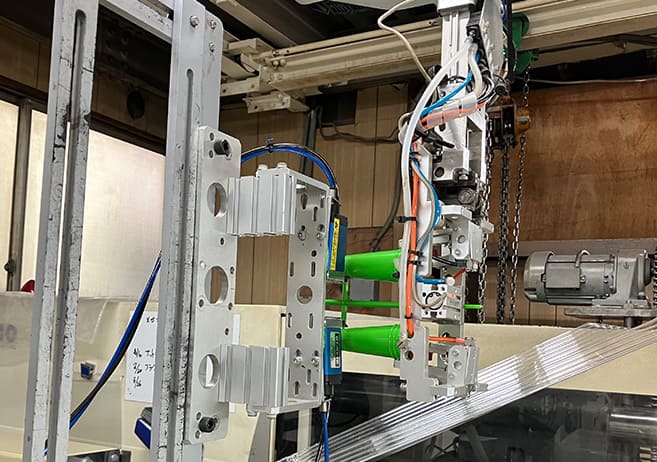
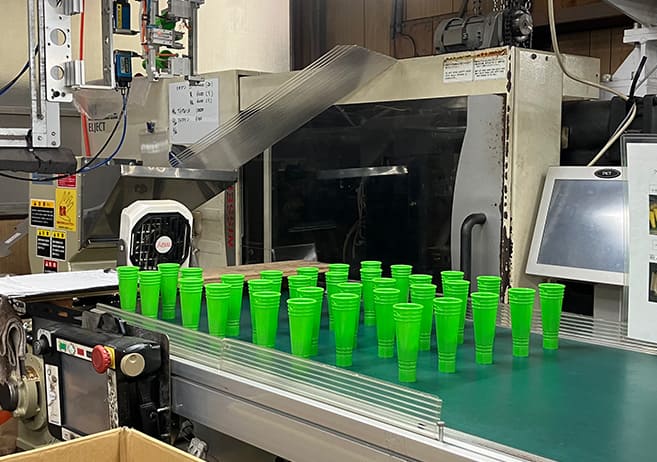
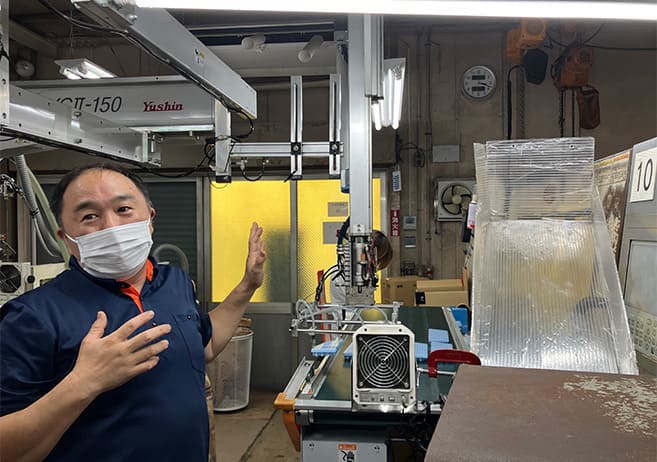
バックオフィス業務をデジタル化
望月氏が次に取り組んだのが、工程管理システムの一元化だ。材料の発注、製品の在庫管理などのバックオフィス業務を1つのソフトで連携し、請求書や伝票などの書類をすべてデジタル化した。中小企業がこうしたIT系のシステムを新たに導入する場合、社員への教育も課題になるが、もともと若手の社員が多くを占める富士製作所には決して難しいことではなかった。その一方で想定外だったのが、外部の取引先との調整だった。請求書の電子化を一斉にアナウンスしたにもかかわらず、やっぱり紙に戻してほしいという取引先もあったという。業界的にはまだまだ紙文化が根強い。経営者の年齢が高いほどデジタルでのやり取りに抵抗感があるようだ。
「DXを進めるには、新しい成形機の購入費用他に、サーバー等の導入費用がおよそ300万円かかりましたが、当時その部分に助成金は出ませんでした。DXのために確保していた資金はないので知恵と工夫で何とかするしかありません。もし外部の専門家などにお願いしていたら、おそらくこの金額では無理だったでしょう。既存のソフトを活用したり、自分で部品を取り寄せて組み立てたりして、今できることから進めていきました。年間の経費もソフトの更新料の10万円程度で済んでいます」。
2023年に江戸川区産業賞を受賞
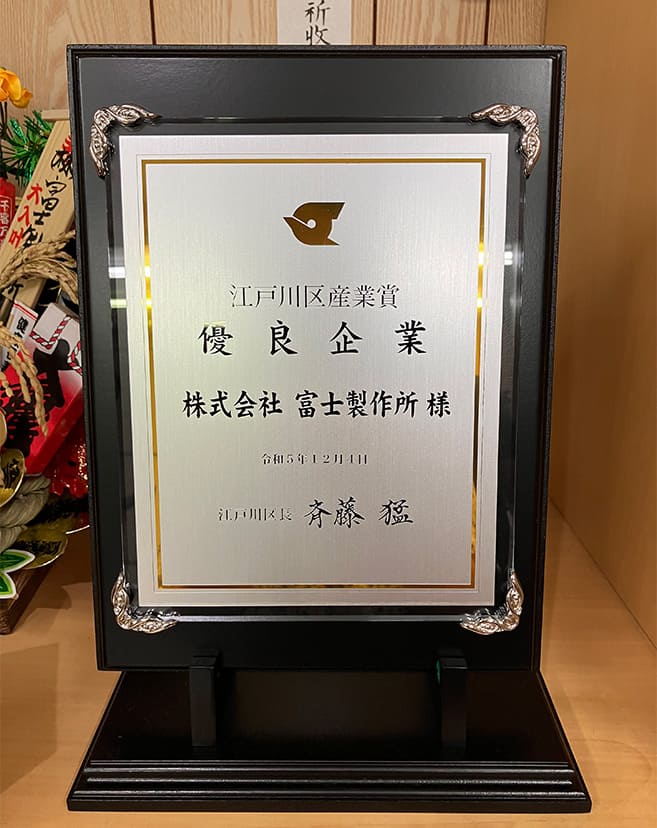
機械の自動化やネットワークの構築によって作業が効率化したことで、かつては常態化していた残業や休日出勤が大幅に減った。さらに、9時から21時の間で作業時間を3時間に区切って持ち場をローテーション化するなど、従業員が作業に集中できる環境も整えた。こうした日々の活動が評価され、2023年に江戸川区産業賞を受賞した。「受賞したからといって何も変わったことはないんですよ」と望月氏は笑うが、富士製作所の取り組みに関心を持った外部の企業からDXの進め方や業務の効率化についてアドバイスを求められることもあるという。
「改善のアイデアが浮かんだらとりあえずやってみることです。やってダメなら他の方法を考えればいいんです。次にやってみたいのは、従業員のシフトを黒板ではなくモニターで周知させるようにすること。常に改善を心がけて良い仕事をしたいですよね」。
飽くなき改善心と見事な発想力で、DX化に成功した望月氏。そのリーダーシップのもとで着実に成長を遂げている工場では、ものづくりが好きな若者たちや地元の主婦の皆さんが毎日笑顔で働いている。常に進化を続ける富士製作所の未来は間違いなく明るい。
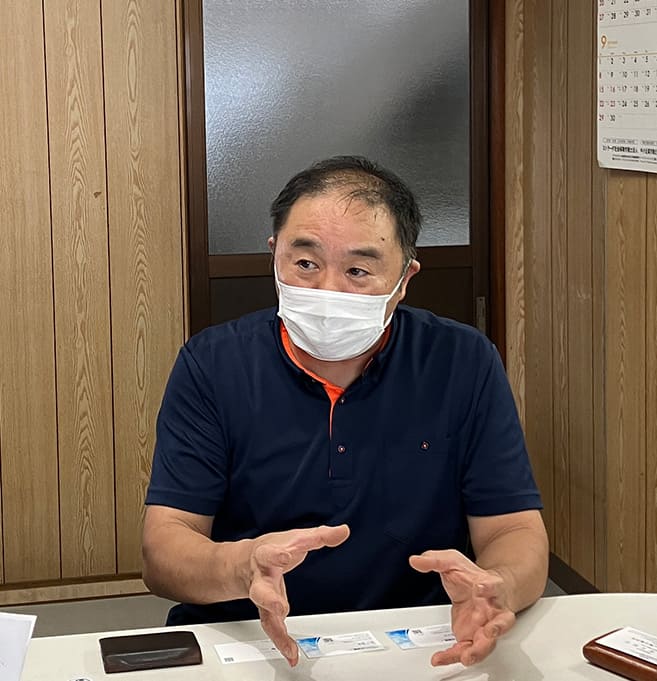
アドバイス
いきなり難しいことをやろうとはせずに、まずは簡単なことから徐々に始めてみることです。FAXをやめてメールにするとか、書類をすべてPDF化するとか、そういう簡単なところから始めてみると良いと思います。最初から誰かに依頼するのではなく、今あるものをどうすれば活用できるかを考えてみてください。
企業情報 | |
---|---|
企業名 | 株式会社富士製作所 |
本社 | 〒132-0034 東京都江戸川区小松川4-71 TEL:03-3636-5608 |
代表者 | 代表取締役社長 望月 新史 |
設立 | 1962年2月 |
資本金 | 10,000,000円 |
従業員数 | 9名 |
URL | https://www.kk-fujiseisakusyo.co.jp/index.html |